Fossil Free Steel: Coming Soon!
Last Updated: Mar 10, 2025If there is one thing we understand here at Rise, it is essential to reduce the built environment's impact on our planet. And if there is one thing we love, it is when traditional building methods and materials are reimagined with this crucial goal in mind.
Steel is a prevalent material used in the construction industry. It is relatively inexpensive, durable, and highly versatile. Iron ore is the main ingredient in steel and needs to be mined for production. This process is incredibly energy-intensive and causes both air and water pollution. Steel production is the most energy-consuming and C02-emitting industrial activity globally, accounting for about 7% of the world's carbon dioxide emissions. It requires an astronomical amount of energy to produce - 20 gigajoules of energy per ton made. As such, the production of steel is considered one of the world's most significant environmental issues.
Steel production companies have become increasingly aware of the energy-intensive challenges of steel production. As such, some companies have been exploring solutions to reduce this environmental impact. HYBRIT is a collaboration between three companies based in Sweden. This team is working together to develop the world's first fossil-free steel.
Table of Contents
- How is Steel Produced?
- How Is HYBRIT Developing Fossil Free Steel?
- Will Fossil Free Steel Cost More Than Traditional Steel?
- What Are the Market Impacts of Fossil Free Steel?
To understand how fossil free steel is made, we first need to understand the primary method of making steel.
How is Steel Produced?
Making steel requires manufacturers to mine iron ore, then melt it in furnaces to remove impurities (such as tar and sulfur), and carbon is added. Other alloying ingredients such as chromium are added to produce various grades of steel, like stainless steel.
Of course, this is a very simplified overview of the complex steel production process. If you are interested in learning more about this process, Purdue University Northwest's Center for Innovation Through Visualization and Stimulation produced an excellent interactive experience of the steel-making process. By learning in-depth about each element of the process, you can better understand how steel production works.
It may come as a surprise that steel has been around for centuries; archeologists have found steel sites about 4,000 years old in Turkey. In the centuries since, the steel-making process has become a lot more high-tech. Today, most steel is made by two methods: blast furnace and electric arc furnace (EAF).
One great thing about steel is that it is one hundred percent recyclable. Scrap pieces of steel can become entirely new material. As such, steel is considered one of the world's most recyclable materials. And yet, it is still an extremely energy-intensive process. In addition, a form of coal called 'coke' is typically used as the carbon input.
How Is HYBRIT Developing Fossil Free Steel?
The HYBRIT steel-making process focuses on becoming fossil-free. And, they have discovered a way to do it! First, the team incorporates fossil-free hydrogen to remove oxygen from the iron ore. Then, they use fossil-free electricity during the smelting process and non-fossil additives instead of carbon. They hope to have fossil-free steel available on the market as early as 2026 and are currently in the pilot-scale research and development stage. Their next step is to create a 'demonstration plant' to illustrate fossil-free steel production on an industrial scale.
This technology developed by HYBRIT can decrease Sweden's total carbon dioxide emissions by about ten percent. The Swedish Energy Agency has provided financial support for HYBRIT, illustrating their enthusiasm for this initiative. The hope is that this work will be scalable and adopted by other countries worldwide, especially as countries strive to reach the climate goals set for 2045 in the Paris Agreement.
You may be interested in who the key players are in this innovative initiative. HYBRIT is a collaboration between companies, each who owns a third of HYBRIT: SSAB, LKAB, and Vattenfall, who together create the HYBRIT consortium. SSAB is a global steel company that specializes in high-strength steel. Always striving for excellence, their steel production process is currently considered the most efficient in the world. Still, they want to make it even more efficient by going entirely fossil-free. LKAB is a global supplier of sustainable iron ore, minerals, and specialty products. Vattenfall is a producer and seller of electricity and heat in Europe. Together, these three companies represent three parts of the value chain.
Will Fossil Free Steel Cost More Than Traditional Steel?
While we do not know the cost of fossil-free steel quite yet, as it is not currently on the market, SSAB has shared that they believe fossil-free steel made with HYBRIT technology will be cost-competitive with traditional steel.
Shop All Special Offers
Shop Special Offers on vetted Home Improvement products at low prices while supplies last.
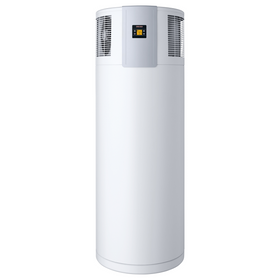
Stiebel Eltron Accelera 300 E Heat Pump Water Heater
Stiebel Eltron
In Stock

Victory Range Hood Sunset 600 CFM White Flush Ceiling Mount Dimmable LED Range Hood
Victory Range Hoods
In Stock
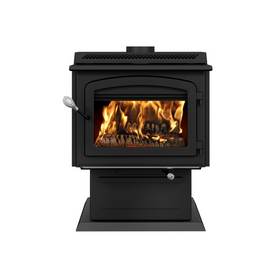
Drolet HT-3000 Wood Burning Stove DB07300
Drolet
In Stock
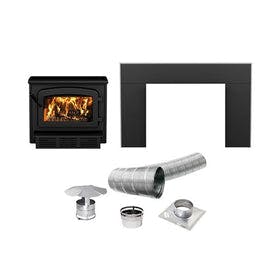
Drolet Escape 1800-I Wood Stove Insert Trio (25ft) DB03127K
Drolet
In Stock

Victory Range Hood Sunset 600 CFM Flush Ceiling Mount Dimmable LED Range Hood
Victory Range Hoods
In Stock

Drolet Escape 1800-I Wood Insert Trio (35 FT) DB03128K
Drolet
Out of Stock

Drolet Escape 1800-I Wood Insert DB03125
Drolet
In Stock
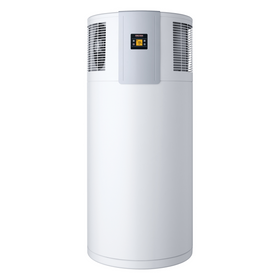
Stiebel Eltron Accelera 220 E Heat Pump Water Heater
Stiebel Eltron
In Stock
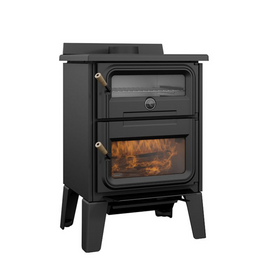
Drolet Bistro Wood Burning Cookstove DB04815
Drolet
In Stock

Quickscrews Cabinet Install Screws
Quickscrews
In Stock
What Are the Market Impacts of Fossil Free Steel?
While the HYBRIT technology is being tested and developed in Sweden and Finland, SSAB Americas shared that come 2026, they plan to produce fossil-free steel in North America. As a significant steel user in the built environment, the environmental benefits of using fossil-free steel in North America could be enormous.
The impacts of fossil-free steel could go well beyond the construction industry. For instance, SSAB and The Volvo Group (headquartered in Gothenburg, Sweden) recently signed an agreement to collaborate on the world's first vehicles made with fossil-free steel. This advancement in the automobile industry could have a trickle-down effect on other sectors that often incorporate steel, such as medical devices, home goods, and art.
In addition to the HYBRIT consortium, other global leaders in the steel industry are looking for ways to improve their steel production processes to lower their overall environmental impacts. For example, the company Voestalpine is striving for carbon-neutral steel, and they promote transparency on their sustainable practices and ecological impacts. Likewise, a German steel-making company called Salzgitter has shared that they aim to cut their carbon emissions by 25% by 2025, 50% by 2030, and 90% to 95% by 2050! Many other steel companies have similar goals. We are looking forward to seeing how this market develops over the next decade. Cheers to fossil-free steel coming soon!
Maria Saxton
Located in Roanoke, Virginia, Maria Saxton holds a Ph.D. in Environmental Design and Planning from Virginia Tech. She works as an Environmental Planner and Housing Researcher for a local firm specializing in Community Planning, Architecture, Landscape Architecture, and Historic Preservation. Her dissertation explored the environmental impacts of small-scale homes. She serves as a volunteer board member for the Tiny Home Industry Association.