ICF Construction: Everything You Need To Know
Last Updated: Dec 30, 2024Insulated Concrete Forms (ICF) are becoming a more common way to build homes. This innovative building material is typically made of blocks of polystyrene foam with space in between to pour a concrete wall. Historically most commonly used for foundation walls, many builders are now taking ICF further and using them for above-grade walls of 1, 2, and 3 story homes.
Table of Contents
- Is ICF Used In New or Existing Projects?
- What is ICF?
- Is an ICF Wall a Good Insulator?
- Is ICF Construction Less Expensive?
- How Much Does ICF Save Over Time?
- What is the Maximum R-Value of an ICF Wall?
- How Long Does ICF Last?
- Does ICF Need a Vapour Barrier?
- Energy Comparison of ICF vs. Wood-Frame Homes
Is ICF Used In New or Existing Projects?
ICFs are found mainly in new construction rather than retrofitting projects. They are easy to install and have several advantages, including strength, durability, and the ability to be well-sealed and well-insulated.
But just how sustainable are insulated concrete forms? Concrete requires more energy to produce compared to conventional wood-framed construction. However, operational energy also plays a significant role in the environmental impact of a building throughout its lifetime. In this article, we'll investigate the environmental effects of ICFs by examining the life cycle of this building material.
What is ICF?
Insulated concrete form (ICF) is a system of expanded polystyrene (EPS) rigid insulation blocks separated by plastic webbing. It is used as an integrated concrete form to pour a concrete wall instead of a traditional wood plank or plywood form. ICF blocks come in interlocking sections, so a wall system fits tightly together. Once the blocks are in place, concrete is poured, and finishes like drywall and siding are attached to fastener strips embedded in the insulation.
Several steps of the construction process are made quicker because the insulation and fastener strips are included with the ICF blocks. ICF walls are typically between 6" and 12" thick. Wall thickness is often impacted by the soil condition and the amount of support that the overlying parts of a building require.
Fun fact: Werner Gregori, a Canadian contractor, filed the first patent for an insulated foam concrete form in 1966.
Is an ICF Wall a Good Insulator?
The short answer is yes, but you need to look a bit further if you build a sustainable, high-performance home. ICF construction has two advantages in terms of the energy performance of the building. First, it seals very well, preventing air leakage through the walls. Second, it has two continuous insulation layers, one inside and one outside, with no thermal bridges. That reduces heat loss.
Is ICF Construction Less Expensive?
Insulated concrete forms cost about $150 per square foot, which is 2% to 7% more than standard wood-frame construction. Overall, you'll likely end up spending about 5% to 10% more in total construction costs than you would for a conventional wood-frame home. Do keep in mind that the price of concrete can fluctuate, and the price of your home is also dependent on the design, local construction labor costs, and additional factors.
It is also important to remember that the amount of time required to compile all of the necessary permits for an ICF home will likely take longer than for a conventional home. Since this is not the standard in the residential construction industry, the permitting process can be a bit more arduous. A licensed builder will likely be familiar with this process to make it a smoother (and hopefully quicker) experience. And, for those DIYers out there, ICF homes are not something that we would recommend attempting yourself if you are not a licensed professional.
How Much Does ICF Save Over Time?
The savings and payback of an ICF home are primarily dependent on what you are comparing to and how well the home is built. If you have a home with an extremely tight building envelope, you will likely experience more considerable savings. While you will probably pay 5% - 10% more upfront for an ICF home, your energy bills will be lower each month than if you were to build a wood-frame home built to typical standards. Industry leaders share that if you compare the initial cost of an ICF home to the utility savings over time, it costs the same as a wood-frame home. But, again, this is dependent on a variety of factors.
What is the Maximum R-Value of an ICF Wall?
ICF construction has two advantages in terms of the energy performance of the building. First, it seals very well, preventing air leakage through the walls. Second, it has two continuous insulation layers, one inside and one outside, with no thermal bridges. This tight building envelope dramatically reduces heat loss.
Shop Sales On Rise
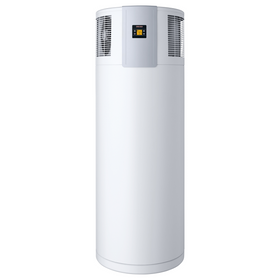
Stiebel Eltron Accelera 300 E Heat Pump Water Heater
Stiebel Eltron
In Stock

Victory Range Hood Sunset 600 CFM White Flush Ceiling Mount Dimmable LED Range Hood
Victory Range Hoods
In Stock
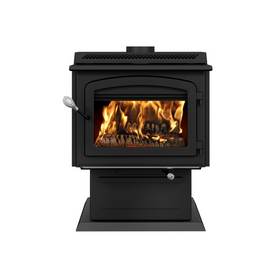
Drolet HT-3000 Wood Burning Stove DB07300
Drolet
In Stock
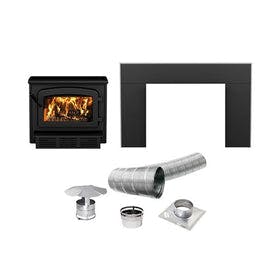
Drolet Escape 1800-I Wood Stove Insert Trio (25ft) DB03127K
Drolet
In Stock

Victory Range Hood Sunset 600 CFM Flush Ceiling Mount Dimmable LED Range Hood
Victory Range Hoods
In Stock

Drolet Escape 1800-I Wood Insert Trio (35 FT) DB03128K
Drolet
Out of Stock

Drolet Escape 1800-I Wood Insert DB03125
Drolet
In Stock
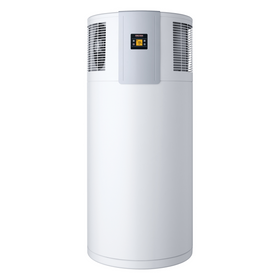
Stiebel Eltron Accelera 220 E Heat Pump Water Heater
Stiebel Eltron
In Stock
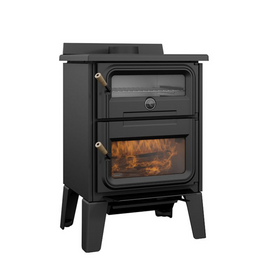
Drolet Bistro Wood Burning Cookstove DB04815
Drolet
In Stock

Quickscrews Cabinet Install Screws
Quickscrews
In Stock
When building a high-performance house, like a Passive House, a typical off-the-shelf ICF system is often not thick enough. It may also struggle to meet the insulation standards in a cold climate like Canada or the northern USA. Fortunately, some ICF manufacturers, like Nudura, have created products with an R-value of up to R-48 to address colder climates.
You can add more insulation to the outside, especially for a foundation, as Phil Dennis did in his Gaspereau Passive House with four extra insulation inches.
On the above-grade walls, adding extra insulation to the inside can work better than the outside. And to make it easier, some companies now offer ICF options with thicker insulation. One example is BuildBlock Building Systems, which sells 1" or 2" inserts that attach to the interior of their ICF wall, adding an insulation value of about R-4.2 per inch.
How Long Does ICF Last?
ICF homes have a lifespan of over 100 years, with minimal maintenance required as the foam will not degrade. It is also important to note that ICF homes can add increased protection during natural disasters. These homes perform well in flooding, so they are appropriate for coastal areas. The reinforced concrete also makes them suitable for highly seismic zones. Some builders can even ensure up to a 4-hour fire rating. If you live in an area prone to natural disasters, an ICF home could give you peace of mind.
Because of how durable ICF homes are, it does make remodeling difficult. If you foresee wanting to remodel your home in the future entirely, you might want to consider a more flexible building material.
Does ICF Need a Vapour Barrier?
ICF walls serve as vapor retardants and do not need a vapor barrier.
Energy Comparison of ICF vs. Wood-Frame Homes
ICF Case Studies
Based on multiple research studies, it is apparent that ICF-constructed homes have a lower environmental impact than traditional wood-frame construction.
One study compares the life cycle performance of a 3,600 square foot ICF house with a wood-frame house. The life cycle assessment (LCA) analyzed the following for both of these construction types:
- The embodied energy of building materials
- The construction process requirements
- General maintenance
- Operational energy
- Disposal of the building materials
- Global Warming Potential (GWP)
The researchers examined two hypothetical homes to address climate differences that can significantly change a building's energy performance. These homes would be built in five geographical locations in the United States and three locations in Canada. The wood-frame house was modeled to follow local building code requirements for each site, and the ICF home followed standards for ICF construction in each location. This approach allowed the researchers to draw meaningful comparisons between standardized buildings.
The study found that across all eight geographical areas, the life cycle performance of ICF homes was better after an assumed life cycle of 70 years. The total energy use reduction of ICF homes was between 4.8% and 12.7%, depending on geographical location and climate. Like other similar studies, this study also found that operational energy use accounts for approximately 90% of a home's environmental impact throughout its lifetime.
Another study compared an ICF building to traditional wood-frame construction and a wood-frame building built to higher than average standards. These researchers found that while the initial energy input required for the ICF building was greater when looking at the entire life span of 100 years, the ICF building had a life cycle energy requirement that was 11% to 14% lower than both of the wood-framed buildings. They also found that the operational energy use was responsible for 95% to 97% of the entire environmental impact for all three buildings.
Yet another study yielded similar results by conducting an LCA of an ICF home and wood-frame home in five US cities representing a range of climate types (Miami, Phoenix, Washington DC, Seattle, and Chicago). They examined a typical size home at 2,450 square feet, which was very close to the average square footage of a single-family home at the time of the study. These researchers also found that the overall environmental impact of wood-frame homes was more significant than ICF homes. The study also provides an exceptionally robust review of construction types, study justifications, life cycle assessment considerations, and discussion of results.
Dave Phelps of ICF Homes of Virginia has witnessed similar results in building ICF homes. "For every three concrete houses we build, it uses the same amount of energy as one wooden house. So if we want to look at energy efficiency for homes, 3 to 1 is an incredible ratio that we can't meet with building houses with wood."
Overall, ICF homes increase your home's comfort, reduce your monthly energy bills, and, most importantly, reduce your environmental footprint. ICF homes are considered high-performing due to their higher thermal resistance and thermal mass, along with stricter construction standards than are typically required for conventional wood-framed homes.
If you build a high-performance home insulated well above code to standards like the Passive House standard, your building will have a much lower energy footprint. That means lower energy bills and even greater sustainability.
Additional Resources
If you choose ICF construction, ask for concrete with fly ash content to use recycled materials. If you decide to go with wood-framed construction, look for FSC certified wood sourced as locally as possible. See our insulation guide to learn more about EPS, blown cellulose, and other kinds of insulation.
Maria Saxton
Located in Roanoke, Virginia, Maria Saxton holds a Ph.D. in Environmental Design and Planning from Virginia Tech. She works as an Environmental Planner and Housing Researcher for a local firm specializing in Community Planning, Architecture, Landscape Architecture, and Historic Preservation. Her dissertation explored the environmental impacts of small-scale homes. She serves as a volunteer board member for the Tiny Home Industry Association.