Biobased Epoxy Resins: A Shift in the Right Direction
Last Updated: Mar 29, 2025Many of our home products, like plastic, are comprised primarily of petrochemicals. These products require fossil fuels to be created and do not decompose readily over time. If they do decompose, it's into microplastics that forever pollute our environment. As we advance the science of our building systems, looking to biobased materials is a critical step in lowering the life cycle footprint of our building materials.
Table of Contents
- What Are Biobased Epoxy Resins?
- What Are Uses for Epoxy Resins at Home?
- Are Biobased Epoxy Resins Environmentally-Friendly?
- Are Epoxy Resins Safe?
- How Long Do Epoxy Resins Last?
- What Are Some Tips For Working with Epoxy Resins?
- How Do You Dispose of Epoxy Resins?
- What Are Some Brands of Biobased Resins?
- Are There Alternatives for Bio-Based Epoxy Resins?
- What Are the Pros of Biobased Epoxy Resins?
- What Are the Cons of Biobased Epoxy Resins?
What Are Biobased Epoxy Resins?
Epoxy, a polyepoxide petro-chemical resin composed of polymers, is a widely used resin for various applications. The newest generations of biobased epoxy resins reduce the environmental impact of epoxies by replacing a portion of the petrochemicals with renewable, biobased materials. Biobased components might include vegetable oils, lignin from wood products, tannins, and rosins. Additional ingredients could contain saccharides, terpenes, cardanols, and syringaresinol (a naturally occurring and non-endocrine disrupting bisphenol found in Magnolia trees). Scientists are working on formulations that eliminate bisphenol A (BPA) from epoxy resins.
What Are Uses for Epoxy Resins at Home?
Epoxy has exceptional durability and resistance to abrasion, chemicals, and water damage. Epoxy resins are commonly used to coat basement or garage floors and furniture such as tabletops. Epoxy can be used as an adhesive to bond a variety of materials such as metal and wood. Unlike many other adhesives, epoxy has excellent gap-filling properties. It doesn't need a high degree of clamping pressure for a strong bond. If you have rotting wood, you can use epoxy to seal the wood and increase its service life. Epoxy is used for fiberglass reinforced laminations and to waterproof or strengthen various materials such as plywood.
Are Biobased Epoxy Resins Environmentally-Friendly?
Biobased resins are a step in the right direction for epoxy. However, there is still a long way to go in improving the lifecycle of these products. Most biobased resins currently available are still primarily composed of petro-chemicals with biobased components ranging from 25-50%. Change often comes incrementally, and as our science advances, the biobased contents of our epoxy resins will likely increase. A 30% reduction in petro-chemicals is still a significant milestone for epoxy resins. It substantially reduces the demand for fossil fuels required to produce these products. Other biobased components such as lignin and syringaresinol lessen the need for BPA, which is a toxic substance to humans and the environment.
Some argue, though, that biobased materials such as vegetable oils divert food from the food supply and still rely on fossil fuel, fertilizer, and pesticide-dependent industrial agriculture.
Are Epoxy Resins Safe?
Uncured epoxy resin is a toxic substance, particularly the hardener component. When working with any epoxy resin, take precautions and familiarize yourself with the manufacturer's material safety data sheet. Some products can contain BPA, a known endocrine disruptor. While biobased resins reduce chemicals like BPA, don't let that allow you to become complacent when working with these products.
When working with epoxy resins, always make sure you work in a well-ventilated area and wear a respirator designed to reduce vapors to protect yourself from VOCs. Always wear personal protective equipment such as long sleeves, safety glasses, nitrile, or butyl rubber gloves. After working with epoxy, remove all contaminated clothing and wash your hands and exposed skin with soap and water. It's good to have several pairs of gloves available; if you get too much resin on your gloves, it can spread to unintended surfaces. A solid supply of paper towels in addition to vinegar and isopropyl alcohol helps clean up resin spills. If you take the necessary precautions and follow the resin directions, you can safely work with epoxy.
Once the resin and hardener are mixed and the curing process has completed to a solid and hardened form, they are inert and non-toxic. If you need to sand cured epoxy, you will create microplastic dust. Always wear a respirator and safety glasses and wash your clothes afterward. A vacuum should be on hand to clean up any dust.
How Long Do Epoxy Resins Last?
Unmixed epoxy resins have a long shelf life and can last three years or more if properly sealed and kept in a controlled environment.
Cured epoxy resins are highly durable and will provide an exceptionally long service life. A properly installed epoxy floor can last up to 30 years before recoating will be needed. As an adhesive, epoxy creates permanent structural bonds that will outlast most other adhesives.
What Are Some Tips For Working with Epoxy Resins?
Always read the safety data sheet and manufacturer's instructions before using epoxy resins. Always wear long sleeve clothing, nitrile or butyl rubber gloves, safety glasses, and a respirator that filters out vapors. A standard dust mask will not suffice.
- Epoxy resins need a properly prepared surface to bond to. To prepare the surface, clean off contaminants with isopropyl alcohol and then sand the surface with the grit recommended by the epoxy manufacturer. Ensure the surface is free of dust before application.
- When mixing epoxies, ensure that you weigh the proper ratios of resin and hardener as directed in the instructions. Triple check that you have the correct proportions, or your epoxy will not cure properly. Add the resin to the mixing cup first, followed by the hardener. Then mix with a wooden stick for several minutes until thoroughly mixed, scraping the sides of the container to ensure any bits of unmixed resin or hardener do not remain.
- Epoxy resins require specific temperatures to cure properly. The stated working time on labels will always have a temperature that the working time corresponds to. You can estimate your real working time based on the temperatures you are working in. Cooler temperatures will give you less working time than warmer temperatures. It's best to mix epoxy in small batches. With epoxy, you have a 'working time' specific to each product to manipulate the epoxy before it gels and becomes unworkable. Small batches will ensure you have the maximum working time, as larger batches of epoxy can heat up in containers rapidly and become unworkable. Most epoxy brands have various options for the speed that the resin cures. You can choose hardener speeds based on the complexity of your project and the temperatures you are working in.
- If you are applying epoxy with a roller or brush, you will only get one use out of them. The epoxy will cure to a solid state and be unusable for further applications. It's advised not to re-use the same tools for subsequent batches of epoxy because you can mix the resins from different batches, which can alter your working time. Plastic squeegees are common applicator tools for epoxy because cured epoxy does not stick to plastic. You can re-use them, unlike brushes and rollers.
Building Materials
Shop high-performance building materials that are vetted for benefits to your health, your pocketbook, and the planet.
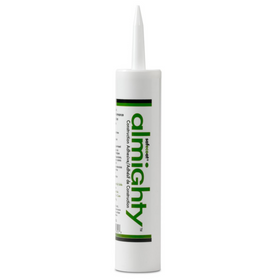
AFM Safecoat Almighty Adhesive Case of 12
AFM Safecoat
In Stock
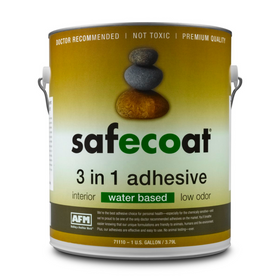
AFM Safecoat 3 in 1 Adhesive
AFM Safecoat
In Stock

Quickscrews Cabinet Install Screws
Quickscrews
In Stock

AFM Safecoat Metalcoat Primer
AFM Safecoat
In Stock

AutoSlide Automatic Sliding Door System
Autoslide
Out of Stock
2 Colors

Autoslide Smart Tag Pet Door Kit
Autoslide
Out of Stock
2 Colors

AutoSlide Elite iLock Smart Tag Pet Door System
Autoslide
Out of Stock
2 Colors

Quickscrews Pan Head Pocket Hole Screws
Quickscrews
In Stock

Autoslide Elite Smart Tag Pet Door Kit
Autoslide
Out of Stock
2 Colors

Autoslide Motion Activated Pet Door System
Autoslide
Out of Stock
2 Colors
How Do You Dispose of Epoxy Resins?
Uncured epoxy resins are toxic to aquatic life, and you must dispose of resins properly. Do not dispose of uncured resins down drains or in household trash. Biobased epoxy resins are not biodegradable!
If you have leftover epoxy, consider donating it or selling it before any attempts of disposal if it's still within its shelf life timeframe. Also, consider other uses you might have for epoxy before disposing of it – it's a useful product. If you have to dispose of epoxy, it's best to mix the resin and hardener at the proper ratios and let it cure. Once cured, you can dispose of it in your household trash. The only reason to dispose of uncured epoxy will be if you don't have a proper resin to hardener ratio to mix correctly.
What Are Some Brands of Biobased Resins?
The USDA BioPreferred certification ensures the epoxy meets the minimum standards set by the USDA for biobased products. Here are a few epoxy manufacturers with bio-based resins:
- Entropy Resins: about 30% biobased, depending on product
- Greenpoxy: 22-52% biobased content depending on epoxy system
- Resin Research Bio Epoxy: 21% biobased when mixed with hardener
Are There Alternatives for Bio-Based Epoxy Resins?
Check out our article on adhesives for alternatives to epoxy if you are looking for adhesives. For furniture and tabletop coatings, consider products from Vermont Naturals as an alternative to epoxy. They offer a variety of products that can be substituted for epoxy coatings.
What Are the Pros of Biobased Epoxy Resins?
Biobased resins are still predominantly comprised of petrochemicals. Also, the biobased contents are mostly under 50% for the available resins, with the majority being in the 20% range. These products are not biodegradable and will break down into microplastics over time. Some argue that biobased ingredients, such as vegetable oils, still rely on a fossil fuel-hungry industrial agriculture system that uses synthetic fertilizers and pesticides.
Biobased resins originally had poor mechanical properties compared to petro-based resins. As chemical science improves, scientists have found that biobased resins that replaced 67% of bisphenol A (BPA) with lignin from pinewood experienced a 25% improvement in flexural strength and stiffness. Another study used vanillin in epoxy combined with a calcium nitrate solution for improved mechanical properties. Biobased epoxies are rapidly catching up to their petro-based counterparts in terms of mechanical performance.
What Are the Cons of Biobased Epoxy Resins?
Epoxy resins can be tricky to work with and apply; you need to be careful of working temperature and wear adequate personal protective equipment. Applications can also create a lot of waste if you are doing multiple coatings and need a new brush or roller for each coat.
Epoxy is often susceptible to UV damage and typically should be painted if used outdoors. It also can soften in high temperatures, so check the technical datasheet for the maximum service temperature of the epoxy if you have a high-temperature application. Once temperatures drop, it will harden back up. These temperatures are typically over 150 degrees Fahrenheit / 65 degrees Celsius, so this might not be a concern for most homeowner applications.
If you are looking for epoxy resins for your home project, consider biobased epoxy resins to reduce your environmental footprint. As our science advances, so too will our epoxy systems. The future is exciting in this realm as we transition away from our dependence on fossil fuel components of epoxy resins - and other home improvement products - and move toward biobased materials.
Tom Saxton
Based in Washington State, Tom's education focuses on holistic land management that sustainably grows renewable building materials in a way that replenishes natural systems. His interest is in building systems that combine old techniques and modern science.