Seven Waste Products Being Salvaged For Your Next Construction Project
Last Updated: Apr 11, 2025One person's trash can be another person's construction material, as innovative companies worldwide find a way to divert tonnes of waste from the landfill. With a bit of ingenuity and some out-of-the-box thinking, items that would have been dumped and forgotten have found new life as insulation, flooring, walls, and more. We gathered some of the most incredible ways these environment-driven makers have reimagined discarded waste into valuable resources.
Table of Contents
- Coffee Husks Become Wall Boards for Prefab Houses in Colombia
- How Can Shredded Plastic Water Bottles Become Foam Wall Panels?
- Old Jeans Become Insulation
- How Can Wine Corks Be Transformed Into Flooring and Wall Panels?
- Natural Bark Finds New Purpose as Siding
- How is Recycled Glass Turned Into Tiles and Countertops?
- How Do Plastic Scraps Get Transformed Into Building Blocks?
Coffee Husks Become Wall Boards for Prefab Houses in Colombia
When coffee beans are roasted, the thin membrane comes off the bean. These discarded piles of coffee husks eventually produce methane, a greenhouse gas that contributes to climate change. However, Woodpecker, a Bogota-based company, discovered that the husks can be transformed into a lightweight yet durable construction material when combined with recycled plastic.
Developed ten years ago, Woodpecker has been incorporating coffee husk fibers to make wallboards. They click together onto steel frames to build prefab houses and schools in remote rural areas of Colombia. Because the country is one of the world's leading coffee-producing companies, these raw materials are readily available.
Once the husks are processed with recycled plastic, the resulting construction material is insect-resistant, affordable, durable, and fireproof – offering the perfect housing solution.
How Can Shredded Plastic Water Bottles Become Foam Wall Panels?
Instead of languishing forever in a giant landfill or the ocean, a construction company is putting millions of plastic water bottles to better use as high-performing building materials for houses and decks. Based in Nova Scotia on Canada's East Coast, JD Composite's structural insulated panels are built with a foam core material consisting of recycled plastic bottles bonded with specialized laminates.
First, Ontario-based company Armacell processes the bottles: After shredding and heating the plastic into small pellets, it is treated with gases and melted into foam. Once it's cool, the hardened foam gets a fiberglass coating, followed by UV-resistant paint. The foam panels then form insulating 5.9-inch-thick walls.
The company recently built a 2,000-square-foot beach house using 620,000 recycled plastic bottles. Not only was it made to withstand Nova Scotia's gale-force winds, but the home is energy-efficient and affordable.
Old Jeans Become Insulation
Natural fibers can make high-performance insulation. Manufacturers have been providing scraps of denim to make insulation for residential and commercial projects, rather than ditching these remnants in the garbage. Old cotton jeans can be used instead of fiberglass or wool between wall studs and ceiling joists, in attics, and anywhere else traditional insulation is applied.
Creating this type of insulation requires much less energy than the fiberglass variety. The denim bits are shredded into loose fibers and treated with a non-toxic, EPA-approved borate solution to improve its fire-resistance rating. It also gets treated to resist mold, mildew, and insects.
Denim scrap insulation offers excellent thermal performance, boosting HVAC efficiency and saving energy, too. You can purchase it in several R-values and sizes to fit snugly into different areas of the home.
While using recycled jeans insulation can be double the cost of fiberglass, this type of insulation provides higher acoustic ratings than traditional products.
The recycled fibers do not off-gas because they do not contain any volatile organic compounds or formaldehyde. At the end of the insulation's natural lifespan, the cotton fibers are then 100% recyclable.
Bonded Logic, a company in Arizona, uses shredded denim to make insulation containing 80% post-consumer recycled natural fibers. The product is packaged into perforated batts, which makes installation more manageable – you tear off only the amount you need.
You can even make your own insulation with a pile of old denim if you have small areas in your home that need a little draft protection. Keep in mind - given the DIY nature of this project, results will vary widely!
How Can Wine Corks Be Transformed Into Flooring and Wall Panels?
Instead of popping the corks from wine bottles straight into the trash bin, several companies recycle them into sustainable building materials.
Since 2008, Cork ReHarvest has collected and recycled billions of corks from across North America. The organization places cork collection boxes in grocery stores. It also offers educational programs to raise awareness about cork forests and works with partners that recycle the corks into different products.
One of its partners, Jelinek Cork Group, which has offices in six countries, is a leader in the cork recycling movement. The company grinds up corks and uses the grain to make flooring, wall tiles, and bulletin boards.
Sustainable Materials, a company based in Colorado, uses post-industrial corks to make mosaic tiles for flooring and wall installations for residential and commercial applications.
Natural Bark Finds New Purpose as Siding
Working with loggers in the plywood and furniture industries, Asheville, NC-based BarkClad, wants to be sure every part of a tree gets put to good use instead of being tossed into a chipper. The company uses trees that were already cut down for other projects and repurposes the bark into wood siding for both interior and exterior applications for homes across North America.
Building Materials
Shop high-performance building materials that are vetted for benefits to your health, your pocketbook, and the planet.
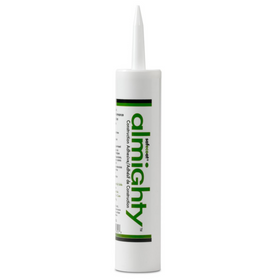
AFM Safecoat Almighty Adhesive Case of 12
AFM Safecoat
In Stock
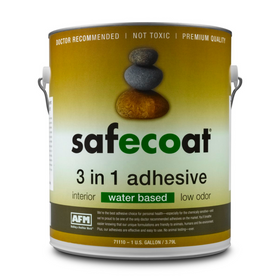
AFM Safecoat 3 in 1 Adhesive
AFM Safecoat
In Stock

Quickscrews Cabinet Install Screws
Quickscrews
In Stock

AFM Safecoat Metalcoat Primer
AFM Safecoat
In Stock

AutoSlide Automatic Sliding Door System
Autoslide
Out of Stock
2 Colors

Autoslide Smart Tag Pet Door Kit
Autoslide
Out of Stock
2 Colors

AutoSlide Elite iLock Smart Tag Pet Door System
Autoslide
Out of Stock
2 Colors

Quickscrews Pan Head Pocket Hole Screws
Quickscrews
In Stock

Autoslide Elite Smart Tag Pet Door Kit
Autoslide
Out of Stock
2 Colors

Autoslide Motion Activated Pet Door System
Autoslide
Out of Stock
2 Colors
Another North Carolina company, Bark House, offers regenerative poplar bark – another waste product of the logging industry – and transforms it into shingle siding and wall tiles. Bark siding can last up to 80 years or more, depending on the type of tree.
How is Recycled Glass Turned Into Tiles and Countertops?
Collecting glass waste from the local window and solar industries, California-based Fireclay Tile handmakes tiles for kitchens and bathrooms. They recapture the water used in the production process and redistribute it to the glaze line or extruders. The company also recycles the waste from cutting granite rocks and reuses its glaze waste into its clay.
Several companies make show-stopping countertops out of recycled glass. Brooklyn, NY-based IceStone has been using glass waste in its products since 2003 and has diverted more than 17 million pounds of glass from landfills.
In Tate, Georgia, Vetrazzo is mixed with composite compounds to create unique artisan counters. Their products are designed to give scrap glass from old jars, car windshields, and traffic lights a new life.
How Do Plastic Scraps Get Transformed Into Building Blocks?
With its goal to recycle 100 million tons of plastic by 2030, ByFusion has big dreams. It developed a building material called RePlast to create an inexpensive modular product. The product can be used for all kinds of construction projects, including retaining walls, furniture, outdoor sheds, fences, furniture, and more. They use a carbon-neutral, non-toxic manufacturing process where the discarded plastic is shredded, superheated, and then fused into blocks.
The final product generates 41% fewer greenhouse gas emissions than concrete blocks. ByBlock is said to be the first construction-grade building material crafted entirely from recycled plastic waste. Unlike concrete, it won't crack, and the product doesn't require any glue.
Wendy Helfenbaum
Wendy Helfenbaum is a Montreal-based journalist and TV producer whose work has appeared in many outlets including Apartment Therapy, Metropolis, Architectural Digest’s AD Pro, AARP, Costco Connection, Country Gardens, Realtor.com, Style at Home, Canadian Living and many more. Follow her @WendyHelfenbaum