Shipping Container Homes: A Recap of ULI’s Thinking Inside the Box
Last Updated: Apr 13, 2025Keiona Cook is getting ready to realize her vision: building a live-work studio in North Minneapolis using shipping containers. Cook has done her research. She started with tiny houses, which led her to shipping containers. She became enthralled. She’s drawn a plan and designed her live-work structure utilizing five containers, including an upper one with a green roof, and two ground-level containers connected by a large expanse of glass.
Her goal is to consolidate her business. Lovely Sewing & Arts Collective, a nonprofit organization through which she teaches sewing, yoga, public speaking, and entrepreneurship to boys and girls ages 4-14—her office and her home in one location. This is why she’s attending a panel discussion on modular and shipping container structures in St. Paul sponsored by the Urban Land Institute (ULI), Minnesota, called “Thinking Inside the Box.”
Building a home using shipping containers is appealing, at least in theory. Millions of excess shipping containers are stacked—unused—near ports around the world. Their size makes them the perfect starting point for a home. Modular in form, they can be stacked, placed side by side, sited to create a U-shape with a courtyard or used in an L-shape. Whether off-grid, in the woods, or the city, shipping containers as a form of hybrid architecture are appealing to homeowners across the United States.
Cook is ready to see what she can learn at the ULI event. She has hours of research under her belt, and multiple visits to the City Planning Department to complete her pro forma and investigate the permitting process. Her eye is already on an urban infill lot, a contractor and architect selected, and with a friend with experience building shipping containers on board.
Case Studies: Modular Hotels, Cargoarchitecture
The ULI event opened with two case studies: citizenM Hotels, which utilize modular construction, and the Detroit-based Three Squared Inc.’s innovations in “cargo architecture.”
Table of Contents
- Spectacles and Sustainability
We spoke to Nathan Jenkins, Market Executive for Mortenson Construction, about the first fully modular hotels in North America. He described how fully kitted, steel-framed units built and shipped from Poland are being used to build it. Stacked like Lego blocks, the modular units that make up a citizenM hotel are bringing a unique construction method to the U.S. that’s fast and cost-effective.
In a slide comparing modular and site-built construction from an environmental standpoint, Mortenson posited a positive impact (meaning a decrease) in the amount of construction waste produced through modular construction. The company also proposed less life-cycle greenhouse gas (GHG) impacts due to less on-site traffic. This was indicated in an additional slide showing the impacts of a typical urban construction site with
- 250 workers per day
- 5,000 private-vehicle round trips
- 120 material delivery vehicle round trips
- 120 hours of idling vehicles
- 12 porta-potties emptied every day
- 360 cubic yards of mixed construction waters
- 4,000 Starbucks cups.
The environmental costs of transporting the modules from Poland were mitigated only, Jenkins later explained, by putting all of a hotel’s modules in one shipment. Mortenson also partnered with the facility in Poland, he added, as the manufacturer had the experience necessary. No suppliers, he contended, exist in the U.S.
Breck Crandall, a Lead Designer for Three Squared, discussed how his firm uses revolutionary technology and steel shipping containers, which naturally meet all building codes. Break says, “to build eye-catching yet durable mixed-use spaces, condominiums, and apartment complexes at a significantly lower cost than lumber cookie-cutter construction.” He discussed how the containers could be clad in wood or brick to help match new homes blend into the existing residential context.
He also noted the speed with which a home or multifamily residence can be constructed. As an example, Three Squared’s 2,800-square-foot Model Center, where the firm has its offices, was erected in six hours and 15 minutes in 2015. The center has two open-concept units with exposed steel inside to show prospective homeowners; a two-story, two-bedroom unit, and a one-bedroom unit on the third floor. Both have striking balcony spaces made from containers.
A blower test, he said, found that shipping containers were as wind and watertight as expected; only the doors and windows needed to be sealed. Spray-foam supplemented with extra insulation brought the R-values of the units to R19 in the walls and R30 in the ceilings, exceeding recommended R-value levels for the climate.
Building Materials
Shop high-performance building materials that are vetted for benefits to your health, your pocketbook, and the planet.
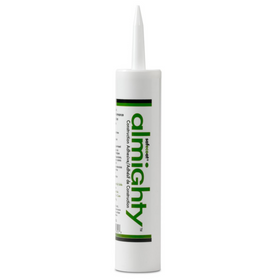
AFM Safecoat Almighty Adhesive Case of 12
AFM Safecoat
In Stock
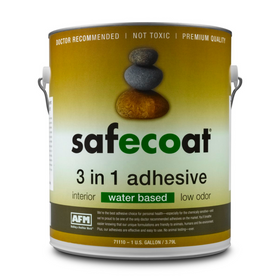
AFM Safecoat 3 in 1 Adhesive
AFM Safecoat
In Stock

Quickscrews Cabinet Install Screws
Quickscrews
In Stock

AFM Safecoat Metalcoat Primer
AFM Safecoat
In Stock

AutoSlide Automatic Sliding Door System
Autoslide
Out of Stock
2 Colors

Autoslide Smart Tag Pet Door Kit
Autoslide
Out of Stock
2 Colors

AutoSlide Elite iLock Smart Tag Pet Door System
Autoslide
Out of Stock
2 Colors

Quickscrews Pan Head Pocket Hole Screws
Quickscrews
In Stock

Autoslide Elite Smart Tag Pet Door Kit
Autoslide
Out of Stock
2 Colors

Autoslide Motion Activated Pet Door System
Autoslide
Out of Stock
2 Colors
The firm’s Cargominium, a 17,250-square foot, 26-unit apartment complex, is the largest container apartment project in the U.S., erected in just under six days. The 2,600-square-foot Ebeling House in Bruce TWP, Michigan, went up in six hours in temperatures below zero. The Grixdale Pocket Houses in Hazel Park, Michigan, were designed for long, narrow infill lots—perfect for shipping containers. Another of the firm’s projects is the Detroit Shipping Co., a restaurant collective and beer garden with restaurants, bars, space for start-up retailers, and galleries featuring local artists.
Spectacles and Sustainability
Breck also talked about how container homes are catching on. “It’s cool, it’s trendy, and it’s a spectacle. To watch a building materialize in a couple of hours is just fantastic.” He also touted the more sustainable aspects of building with shipping containers. “Over one million shipping containers are lying idle, clogging U.S. ports and landfills,” he said. “Three Squared has met or exceeded all building and safety codes to date and provides a cost-effective, sustainable building alternative.”
Electric heat pumps, roof condensers, and mini-splits were discussed as sustainable options to include in a shipping container home. Everyone on the panel agreed that cities and their residents have a long way to go in accepting both modular and container architecture, even more so in the U.S. Midwest. This included James Garrett, Architect and Principal with 4RM+ULA Architects, and Christian Lawrence, Founder and CEO of Rise Modular.
Garrett talked about how technology is enabling homeowners to secure loans online, challenging traditional lenders who need to catch up. He also mentioned how a generational transition in city leadership is allowing fresh ideas with hope for new and innovative building classifications. Lawrence brought up the fact that less market risk exists with the modular construction of multifamily residences or hotels, as revenues can be earned faster. Jenkins referred to this as “heads in beds.”
Moving Forward
Education, however, remains a constant: The need to educate city officials, developers, lenders, homeowners, and other architects about the potential in modular and container housing. As for Cook, she’d like to see her dream realized in the six to eight months. She’s ready to move from her traditional apartment into an innovative live/work building constructed of shipping containers. This will give her unique non-profit organization a home in a building she hopes will inspire other homeowners in her community.
“In all of my research, I loved seeing couples and individuals living in container homes that they envisioned,” she says. Shipping containers, she says, have become her passion. “I realized I too could build an efficient home, with shipping containers as my go-to construction method. For me, it’s the way to go.” With that, she’s off to question the panelists about insulation, permits, design, and to realize her vision.
Camille LeFevre
Camille LeFevre is an architecture and design writer based in the Twin Cities.