- Home
So, it was only a matter of time before Spohn and his wife Marilyn decided to "walk the talk" and build their own sustainable forever home. As children of Depression-era parents, they grew up with an understanding of economic hardship. They learned how to work hard and save. They were also reminded to respect and wisely use the earth's natural resources. By the time he left college, Spohn knew he'd be working in an energy-related profession.
In 2019, the couple began planning their new 4,480-square-foot home on three acres just outside of Pittsburgh. In November 2020, they moved into their solar-powered, net-zero, modular home. Spohn writes about the design and construction processes on his blog, Spohn Home, to encourage like-minded folks to follow into his journey. The blog posts, he writes, intend to provide readers with insights and inspiration for making the changes necessary to combat climate change as we continue to build and operate homes.
Why Modular?
Prefabricated modular houses are built in a factory, then delivered to the building site for assembly. The factory-built modules can be end-to-end, side-by-side, stacked, or any combination based on the design. The modules are tied together with inter-connections that keep the sections in place.
"Modular was immediately appealing because it's factory-made, and all of the materials are inside and protected during construction, which is great for future durability," Spohn says. He also liked that the same crew worked on the modules every day, that the process is efficient with minimal waste, and includes ongoing quality control. Using laser alignment to keep things square for easy assembly, Spohn adds, the crew worked on the modules "from all six sides, from inside and out, and underneath and on top," for rapid, thorough, and well-integrated construction.
EcoCraft Homes in Pittsburgh and Structural Modulars, Inc., in western Pennsylvania, collaborated on the four modules for the Spohn home. "Those two companies have worked together for 15 years," Spohn says. "The boxes were built from the inside walls out, which is an important factor in home performance when it comes to airtightness," Spohn says.
The four boxes are each 14 feet wide, 11 feet tall, and 64 feet long. From the interior to the exterior, the high-performance wall construction includes drywall, 2x6 stud on 24-inch centers, and R-19 fiberglass insulation. Next came a ZipSystem® air-sealed sheathing system applied to the framing, with putty put over every fastener head for air sealing and for moisture resistance. A 1.5-inch layer of graphite-impregnated EPS rigid board followed, with tape and sealant at the seams to cover all the gaps for airtightness. Next was a weather-resistant barrier, and finally an upper-grade vinyl siding as the cladding.
Deep bays on the upper floor allowed for fiberglass and blown-in cellulose insulation to reach R-45. The homeowner selected a moisture barrier that lets moisture out but doesn't take it in. "We paid a lot of attention to air sealing—in the factory, while constructing the house onsite, and after blower tests."
The home's foundation, provided by a locally owned company, is precast concrete with 8.5 inches of EPS in a concrete cavity to reach R-30.
Still, many of their priorities were "passive-leaning," including super-tight construction with minimal air changes with the outside; Passive House-rated windows; insulation higher than code; a high-efficiency HVAC system; and minimal thermal bridging.
Their priorities also included good control of temperature and humidity, excellent indoor air quality, low or no VOCs, low energy consumption, and an all-electric home powered by solar power. So, they decided they'd call their new house a "personalized performance home."
They selected a Dettson heating and cooling system with a two-ton air-source heat pump set up for four zones. "I was intrigued with their products for cold climates," Spohn says. The grid-tied, 32-panel, 12-kW solar array was installed by a local vendor, Envinity, which also does sustainable design and construction. The couple found Envinity from the local solar co-op, which is sponsored by the national non-profit Solar United Neighbors.
"We signed on and got a good price from Envinity," he says. "They sized the system with their best guess, going a little bit over to cover an electric car—which we don't have yet. We recently received the annual "true-up" electrical bill. We got a credit for the excess energy since the system went online in July 2020, which means we passed the net-zero threshold for that time. We'll need to look at the data for a full year of occupancy to claim we made it to net zero.
Building Materials
Shop high-performance building materials that are vetted for benefits to your health, your pocketbook, and the planet.
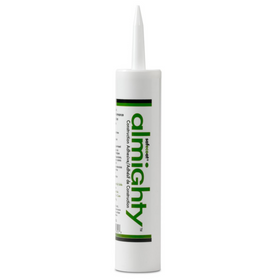
AFM Safecoat Almighty Adhesive Case of 12
AFM Safecoat
In Stock
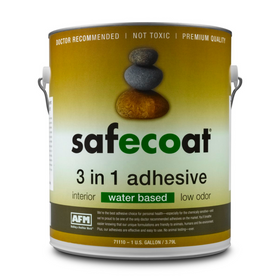
AFM Safecoat 3 in 1 Adhesive
AFM Safecoat
In Stock

Quickscrews Cabinet Install Screws
Quickscrews
In Stock

AFM Safecoat Metalcoat Primer
AFM Safecoat
In Stock

AutoSlide Automatic Sliding Door System
Autoslide
Out of Stock
2 Colors

Autoslide Smart Tag Pet Door Kit
Autoslide
Out of Stock
2 Colors

AutoSlide Elite iLock Smart Tag Pet Door System
Autoslide
Out of Stock
2 Colors

Quickscrews Pan Head Pocket Hole Screws
Quickscrews
In Stock

Autoslide Elite Smart Tag Pet Door Kit
Autoslide
Out of Stock
2 Colors

Autoslide Motion Activated Pet Door System
Autoslide
Out of Stock
2 Colors
Building a Forever Home
The Spohn home is just 15 miles from downtown Pittsburgh, but "we have two neighbors with horses and one who has 100 Alpine and Nubian goats and makes artisan goat cheese," Spohn says. "We love it."
Since moving in, there are few things the couple would have done differently. They're currently working on planting a native wildflower meadow and are enjoying their outdoor flagstone and crushed limestone patio.
They made sure the house would accommodate them as they age. When the time comes, they can live on the first floor, which has a bedroom, a zero-entry shower, ADA-wide doorways, and pocket doors. With ample room for their kids and grandkids to visit, the Spohns have settled into their high-performance forever home.
"We were looking for where we would retire," Spohn says. "We decided it would be here. We've built an energy-efficient home just for us where we can age in place and enjoy our family for years to come."
Camille LeFevre
Camille LeFevre is an architecture and design writer based in the Twin Cities.